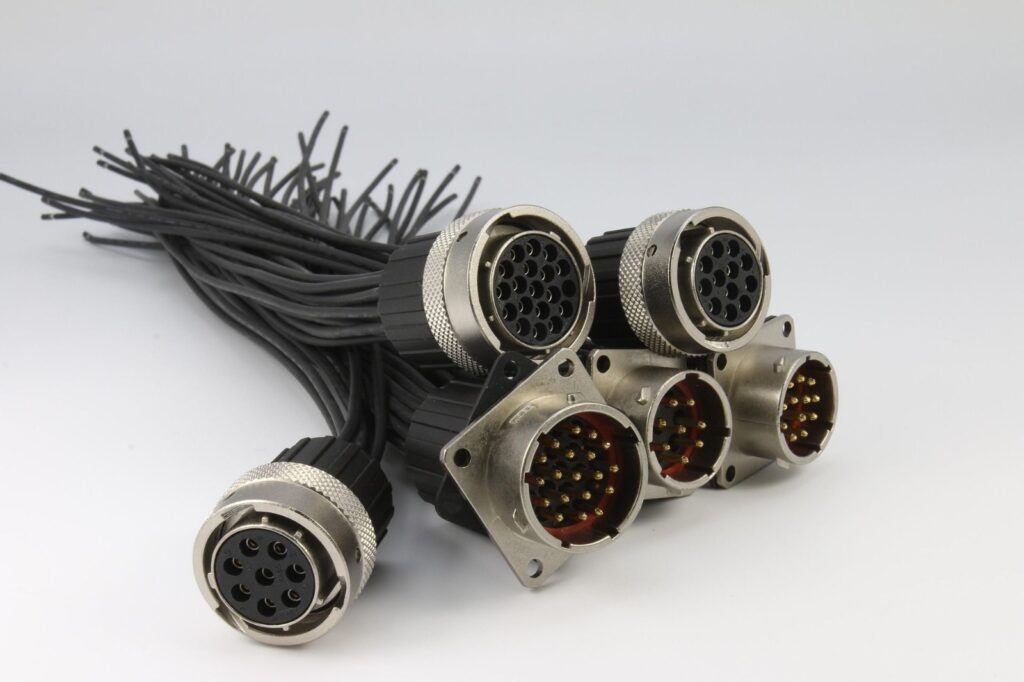
Lightweight, cost-effective, and corrosion-resistant, aluminium connectors are a preferred choice for a range of industries from automotive to aerospace to railways.
However, one key process that has an impact when it comes to performance and longevity is electroplating.
Why Electroplating in Aluminium Connectors matters –
Aluminium naturally forms an oxide layer that resists corrosion, but that same oxide also resists electrical conductivity and plating adhesion. That’s where electroplating comes in. Electroplating when done well also enhances:
- Electrical conductivity
- Corrosion resistance
- Wear resistance
- Solderability
- Surface aesthetics
For OEMs and other industrial applications, this directly translates to better signal or power integrity, longer product life, and lower maintenance costs.
A Look At The Electroplating Process
Electroplating on aluminium isn’t plug-and-play—it demands precision.
- Surface Cleaning & Deoxidation: Aluminium’s oxide layer must be removed using acid etching or alkaline cleaners.
- Zincate Process: A thin layer of zinc is deposited to allow subsequent plating to adhere—this is a make-or-break step.
- Underplating: Often a layer of nickel or copper is applied before the final finish.
- Final Plating: Choices typically include tin, nickel, silver, or gold, depending on application needs.
Choosing the Right Electroplating –
When selecting the right plating finish, understanding the final usage is very important.
While Gold and silver platings are expensive but in high-frequency or mission-critical applications, that investment can prevent catastrophic failure. Whereas, in some cases, the end usage is just to maintain a fluidity in the flow of the connection. In such a case, the type of plating doesn’t bear much significance.
The team may inquire about the following parameters –
- Is signal integrity critical?
- Will the connector be exposed to extreme temperatures or humidity?
- Is mating/unmating frequent?
- Are there budget constraints?
Why Electroplating is Critical
While aluminium connectors are lightweight, non-magnetic, its’ surface characteristics demand careful preparation before use in high-reliability electrical applications. The naturally forming aluminium oxide layer:
- Is electrically non-conductive
- Inhibits the adhesion of plating materials
- Reacts adversely with certain plating baths
This makes electroplating an important activity in manufacturing these connectors. Some of the popular plating that are normally used in industrial applications are as follows –
Nickel Plating
Application Conditions:
Connectors that are subjected to high current loads, vibration, wide temperature swings, and significant environmental exposure (moisture, dust, and pollutants). Like in the case of industrial connectors operate in environments with oil, chemical vapours, mechanical wear, and temperature extremes. In many cases, connectors remain mated for long periods but must be reliable under harsh conditions.
Why it works:
Nickel’s barrier properties reduce galvanic corrosion when mated with dissimilar metals—a common concern in railway connectors. Tin, while softer, is suitable when cost constraints dominate and frequent mating is not required.
Silver or Gold Plating
Application Conditions:
Connectors that are being used in places that demand the highest level of performance, such as exposure to high altitudes, thermal cycling, vibration, and strict weight restrictions.
Why it works:
Gold maintains contact reliability even in harsh, low-pressure, or corrosive environments, making it ideal for avionics and spacecraft systems. A nickel underplate prevents diffusion and ensures adhesion. Silver is often preferred for power distribution due to its thermal conductivity, though it needs anti-tarnish treatments or controlled environments.
Electroplating is an engineering decision that affects connector performance across mechanical, electrical, and environmental parameters.
By aligning plating choice with application-specific demands, engineers can optimize reliability, reduce maintenance, and ensure lifecycle compliance.
When selecting aluminium connectors, ensure your supplier follows robust surface preparation and plating protocols, especially for mission-critical applications.